In a warehouse in Harrison, New Jersey, Assembly OSM’s first apartment destined for a real-life project sits waiting.
The one-bedroom unit occupies the middle of the weathered space like two puzzle pieces yet to be fit into the larger picture (both literally and figuratively, as neither the startup nor its partner SHoP Architects would disclose the project’s location or developer).
“We put it together like an Ikea piece of furniture,” said Chris Sharples, co-founder of both Assembly and SHoP Architects, during a recent visit.
He and his twin brother, Bill Sharples, launched the modular construction startup in 2019, aiming to make high-rise construction faster and cheaper.
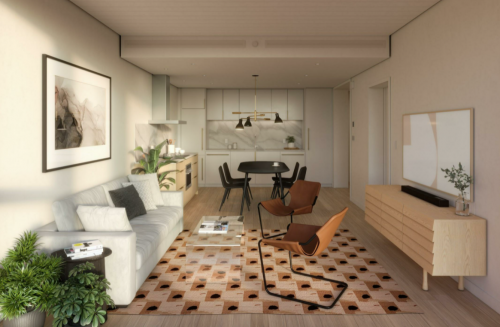
(AOSM)
The premise involves approaching building more like assembling a car, airplane or even a spaceship, with greater transparency around materials, labor, quality, timelines and cost than in traditional real estate development. To deliver on that, the company has tapped engineering talent from the likes of Tesla, SpaceX and Boeing.
Digital models of projects are accessible to suppliers who provide — rather than materials like wood or piping — entire elements, such as bathrooms or kitchens. From there, Assembly’s patented clipping mechanism attaches the pieces to a steel rectangular chassis, stacking units up to 30 stories high like Lego blocks.
The company claims that its approach can reduce the timeframe of a project by 50 percent, cut its carbon footprint by 25 percent and mitigate the generally unpredictable nature of construction. So far, it’s raised $21 million from its believers, including investment bank Jefferies Group.
The company says its model will reduce change orders and budget overruns, and quickly facilitate repairs and upgrades as all components can be removed and swapped out for newer ones as needed.
Read more
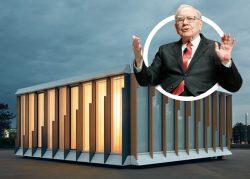
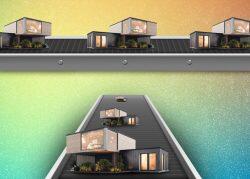
Developer MaryAnne Gilmartin, an advisor to Assembly, said the company’s approach to modular construction is “very different” in terms of both process and quality from what she’s seen previously.
“That’s a condo-level finish,” she said of the model one-bedroom apartment sitting in the J. Supor Industrial Park. “It’s next-generation.”
Though Assembly’s first project is with SHoP, the company is independent and its executives said it is willing to avail itself to any developer or architect. Notably, Assembly will have some stock designs, allowing it to perform design-build projects without a developer needing to hire its own architect.
The handful of modular projects built in the city to date have been riddled with construction delays and problems, including 461 Dean Street, the residential tower developed by Gilmartin’s former firm, Forest City Ratner. Katerra, the off-site construction startup backed by Softbank, imploded spectacularly earlier this year.
But Assembly is far from the only startup working at cracking the industry. Warren Buffet’s Berkshire Hathaway is backing a new modular construction company called MiTek, which is being led by another New York-based architect, Danny Forster. Others, such as Veev and Factory_OS, have received funding from the Tel Aviv Stock Exchange and Google, respectively.
Gilmartin admitted that developers may take some convincing, but said that if Assembly can deliver on its promises, “changing attitudes” from unions — which have a history of opposing prefabricated construction materials — have created an industry open to new approaches.
“The next step for this technology is for a building to be built this way and for it to become a proof of concept,” she said.