The new 246-foot-tall CitizenM New York Bowery Hotel on the Lower East Side has set a new bar for hospitality construction. Despite a relatively quiet grand opening in late September, it’s now the world’s tallest prefabricated hotel.
Rob Wagemans, the Dutch hotel brand’s creative director and chief architect, described modular construction — where rooms are made in a factory before being shipped to a job site for assembly — as part of “the DNA of CitizenM.” The “M” stands for mobile, and the 12-year-old hotel chain markets itself as “affordable luxury” for those who are “always on the road.”
“We try, wherever possible, to build our hotels modular,” Wagemans told The Real Deal, saying that there are fewer surprises when it comes to the quality of interior work and the finishes last longer. Eight of the company’s 13 properties throughout Europe and North America were prefabricated, he said, though he doesn’t expect guests to care.
“You will not see the difference,” Wagemans maintained, “but we get a much better product.”
The new hotel is CitizenM’s second in New York City, though the first, in Times Square, was not built with prefabricated rooms.
In the 300-key Bowery hotel, each guest will have 165 square feet of space outfitted with a good shower, “ridiculous” Wi-Fi and an outlet for every charging cord possible, said Michael Levie, the hotel chain’s vice president of operations. Guests, he added, are likely to spend most of their time in the hotel’s red-accented “living room,” which replaces the more traditional lobby and is centered around a cafe and bar.
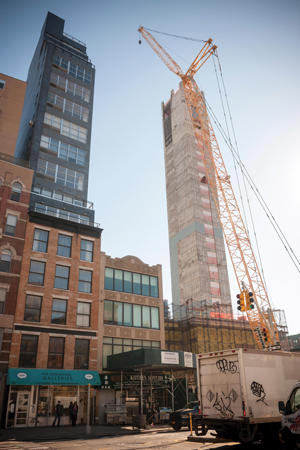
The modular hotel had been scheduled to open in 2017, but was delayed for more than a year due to unforeseen hurdles.
But the 21-story modular is part of a growing supply glut in the city’s hotel market, where an estimated 13,000 new rooms are under construction. Those will come on top of roughly 120,000 existing hotel rooms across the five boroughs, according to industry data provider STR.
“It’s another batch of hotel rooms in a crowded market,” said New York hospitality consultant Stanley Turkel. “They’re paying a lot of attention to improving the environment of the hotel. Will that improve occupancy? Let’s hope so.”
Stacking the odds
Roger Krulak — a former Forest City Ratner executive who now runs one of the few modular construction firms in the city — said CitizenM’s first modular hotel in New York comes as the market for prefabricated buildings is taking off.
Krulak, who runs FullStack Modular out of the Brooklyn Navy Yard, said he’s seeing the most interest in modular construction since he set up shop in October 2016. Over the past two years, his firm has worked with “small developers who were pioneers trying to do great things,” but lately, he said, he’s been fielding calls from Related Companies, RXR Realty, WeWork and Turner Construction.
“The whole dynamic has changed,” Krulak said.
But while more developers are showing interest, only a few modular projects in the city’s residential and hospitality sectors have been completed in recent years.
One of the first was a seven-story rental property in Inwood built by Brown Hill Development in 2013. The $13 million project kicked off a flurry of interest among other developers. Forest City, for one, planned to construct 15 of the buildings at its Pacific Park megadevelopment using modular construction and even launched a division to do it, with Krulak at the helm.
Then Forest City abruptly shut its prefabricated business in 2016, as it began divesting noncore businesses, and the city’s only other modular construction company, Capsys, called it quits after a rent hike at its Navy Yard workspace. To the rest of the world, it seemed like New York was giving up on modular construction, and even lenders took note, according to Krulak.
That was the environment in which CitizenM and its development partner, Brack Capital Real Estate, began work on the Bowery modular hotel. The two firms had the prefabricated rooms manufactured in Poland and shipped to Manhattan, where the installation process kicked off in November 2016. NYC Department of Buildings officials inspected and approved all of the hotel parts in a factory about four hours north of Warsaw before everything was shipped across the Atlantic.
One of the company’s goals is to “change the hospitality industry” the same way fast-fashion retailers Zara and Uniqlo put legacy brands on the defensive, Wagemans said.
But the realities of building a modular hotel in Manhattan proved to be less than ideal.
The hotel, which had been scheduled to open in late spring 2017, was delayed for more than a year due to unforeseen hurdles. The project’s general contractor had a fatal accident on another site, which caused “several months of no work and later a full restart of the construction process,” according to Levie.
“I think in the future, for CitizenM, it will be faster,” Wagemans said. “But building in New York City, to be honest, I don’t think it makes a difference in speed.”
Brack Capital did not respond to requests for comment.
New York boutique hotelier Richard Born of BD Hotels — which opened the city’s first known modular hotel, in Williamsburg, last fall — said he believes CitizenM also had challenges with the height of the Bowery project. Born noted that his Pod BK project and the Bowery project were manufactured in the same Polish factory and said even his four-story hotel experienced an eight-month delay, because of issues with the flooring and waterproofing.
“I would not do a 25-story modular building,” he said.
Krulak, however, said he believes several other modular projects will overtake the CitizenM Bowery’s height in short order and argued that the finished project sets a benchmark for both hospitality and construction.
“It’s a trailblazer,” he said. “[They] started at a time when everyone had doubts, and they forged ahead.”
Rising in the up cycle
The opening of CitizenM’s Bowery modular also comes as the hospitality industry has bounced back from a rough stretch in recent years.
With the economy charging full steam ahead and investor confidence on the up following the Plaza and other big-ticket trades in 2018, the latest projections for New York City’s hotel market have been largely positive.
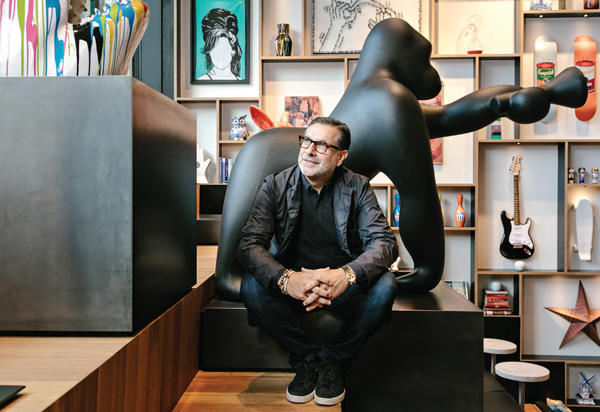
Michael Levie, CitizenM’s vice president of operations, on the hotel’s ground floor
This year, revenue per available room in the city has risen to $215.27 as of September, up from $208 in the same period last year, according to STR. And the city’s year-to-date occupancy rate was 86.7 percent — compared to the national average of 67.7 percent.
But New York’s hotel market remains highly susceptible to a downturn, sources say.
“The macroeconomic indicators wouldn’t suggest it at all, [but] because we’re so long in the up cycle people are worried,” STR Senior Vice President Jan Freitag told TRD. Under such conditions, even a small shock could affect the market, and with occupancy so high in New York, “any downturn will be felt,” she noted.
Born said he’s feeling “cautiously encouraged” by the market’s strong run in 2018 but doesn’t think modular construction will change how a hotel fares in the long term.
“Once the product is built, it doesn’t matter how you built it,” he said.
Anne Lloyd-Jones, who runs the New York office of global consulting firm HVS, said prefabrication has long been synonymous with “low quality” and most commonly used for low-rise, wood-framed hotels. If anything, going modular could cramp a hotel’s performance due to the trend’s “mixed reputation in terms of quality and outcome,” she added.
As dragged-out construction times and overrun budgets become routine in New York hotel development, however, that could quickly change. A TRD analysis this summer found that building hotels in the city takes nearly a year longer than any other asset type. Modular construction, meanwhile, is widely seen as more efficient and less labor-intensive overall.
It helps that the use of modular hotel bathrooms has already gone mainstream: An estimated 20,000 prefabricated lavatories have been installed in U.S. hotels since 2004, according to the trade publication Hotel Management. Lloyd-Jones described that as the industry’s first foray into modular building, but she said Marriott going “all in” really changed the game for hotels.
Last year, the public company began issuing new standards for its Hilton and Holiday Inn brands that allow developers to use either traditional or modular construction to build their hotels. Lloyd-Jones said other companies are following suit, while modular hotels are increasingly “going high-rise.”
But whether CitizenM’s Bowery hotel will further popularize modular construction in the hospitality industry remains to be seen.
Not everyone in New York and beyond will appreciate the significance, said Krulak. While for some it matters a lot, he noted, others just see it as another hotel in one of the world’s largest hotel markets.
For the latter, “it’s like if it were the tallest modular animal hospital in the world,” he said.