For residents of a Milwaukee tower to admire the wood holding it up, samples of the material first had to undergo a trial by fire. Literally.
The U.S. Department of Agriculture burned the glue-laminated timber columns for three hours in a lab, the longest test ever conducted for the material in the states. The 2019 examination helped persuade local officials to grant developer New Land Enterprises variances to build the 284-foot tower with timber and expose more of it than is usually allowed.
The luxury apartment building, aptly named the Ascent, would be the world’s tallest timber structure. That status, however, will be short-lived: Interest in mass timber, an umbrella term for types of engineered wood, is mounting across the United States.
Mass timber is touted as more sustainable than steel and concrete, and as a climate solution in a sector that accounts for an estimated 40 percent of greenhouse gas emissions globally. It also can speed up construction timelines because many of its components are prefabricated.
“There are very few adjustments that you have to make in the field,” said Tim Gokhman, managing director of New Land. “The ability to repeat, but also to design upfront, and have it be so precise is unlike anything else.”
U.S. cities are just starting to explore the possibilities of manufactured wood. They are far behind Europe and Canada, where dozens of such buildings have sprung up and more are coming. Last year, French President Emmanuel Macron promised to pass a law by 2022 mandating that publicly financed building projects be at least 50 percent wood or other organic material. Naples, Italy, is constructing a train station under that standard.
The material has held up against not just fire but other simulated disasters, sparking optimism among developers, architects and public safety officials. Still, there is much to learn about mass timber before it becomes ubiquitous in high-rise construction.
Because the industry is immature in the U.S., it lacks manufacturing capacity and standardization of building components. That means the material, as well as design and construction services, comes at a premium. The higher costs will deter some developers.
“Everybody loves the idea of a 25-story mass-timber building. It captures your imagination,” said Iain Macdonald, head of Oregon State University’s TallWood Design Institute. “But that is not typically how developers make their money.”
Navigating the rules
In January, the International Code Council published new guidelines for timber towers, blessing projects as tall as 18 stories, up from six. States and cities model their codes after the council’s standards — some much more aggressively than others.
Oregon adopted the changes in 2018, when they were still in draft form. New York City is at the opposite extreme: It is in the process of implementing the council’s recommendations of six years ago.
One problem mass-timber advocates have with the international body’s new recommendations is that the higher a building goes, the less wood can be exposed without special permission. At 18 stories, none can be visible.
“That’s a deal-breaker,” said John Peronto, senior principal and co-director of the Chicago office of engineering firm Thornton Tomasetti, which performed structural design services for the Ascent. “Not only do you have to buy all the drywall, but then you have to cover up all the beautiful wood.”
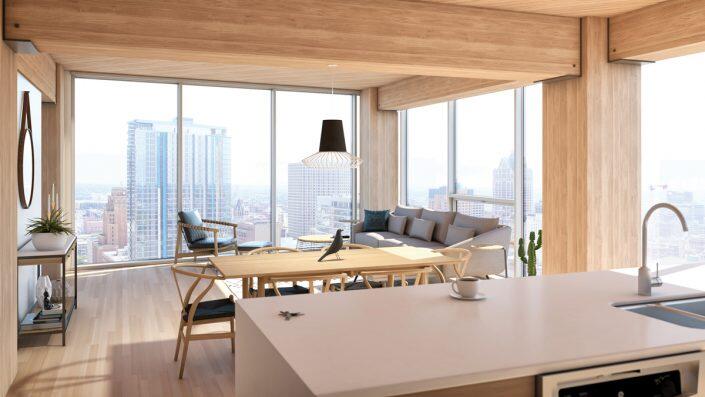
Residents will be able to see the Ascent’s exposed wood columns.
The new code recommendations have been adopted more quickly in locations with robust timber industries, including Washington, Oregon, Utah, Idaho, Maine and California. New York City, where construction with cross-laminated timber is forbidden, is considering allowing it, but only up to six stories. That would severely limit its potential.
(Editor’s note: The New York City Council in October 2021 approved a change to the building code allowing cross-laminated timber on projects up to 85 feet tall, or six to seven stories.)
The city’s Department of Buildings Commissioner Melissa La Rocca defended the lengthy and cautious revision process, saying it looks at the city’s “very specific needs,” given its mix of density and aging building stock.
“To compare us to others would be imperfect at best,” she said. “I think this is a very good, solid step for the city.”
Tanya Luthi, vice president at engineering and design firm Entuitive and a member of New York City’s structural code committee, advocated for the expansion of mass timber. She noted that the national conversation about it has evolved considerably, but there is still resistance to shifting away from materials that the industry is accustomed to, namely steel and reinforced concrete.
“I have heard in code committee meetings a lot of fear. I think a lot of that fear is based on an unfamiliarity,” she said. “I think in New York there is still a bit of an uphill battle.”
Other reasons for New York’s incremental approach are the lack of a nearby timber industry to pressure it, and a feeling that going from a total ban to something higher than six stories would be too much of a change.
In that context, the jump to 18 stories represents a quantum leap for the traditionally conservative international body, said Kenneth Bland, vice president of codes and regulations at the American Wood Council.
“It is very difficult to change the number of stories, and heights, for any type of existing construction,” Bland said. “It is going to be a long time until we see the code change, I’d speculate.”
Costs and benefits
A pandemic may not seem like the best time to take risks, especially in the office market. But Waterstone Properties is moving forward with plans for Maine’s first mass-timber commercial building, which will rise six stories.
“We love being at the forefront of change. But you have to be smart when you are first,” said Greg John, chief marketing officer at Waterstone. “We almost feel we found this secret that is not going to be a secret for much longer.”
That office and retail building will be part of Waterstone’s planned 1.3 million-square-foot, mixed-use development in Westbrook known as Rock Row. John said the company is confident that tenants will be drawn to the material’s beauty as well as its properties as a natural insulator, energy saver and even air circulator.
Climate-minded tenants may also be impressed by the material’s smaller carbon footprint. A 2019 study by the University of Washington projected that hybrid cross-laminated timber buildings — which include other materials, such as concrete or steel — could reduce “global warming potential” by more than 25 percent.
Cement and concrete production contribute about 8 percent of the world’s greenhouse gas emissions, as does the steel industry. Proponents of timber construction portray it as “sequestering” carbon — storing it in a building rather than releasing it into the atmosphere.
However, much depends on sourcing the timber to ensure that it isn’t contributing to clear-cutting. Macdonald said that selecting less popular wood types, and thinning excess wood fiber that would otherwise be kindling for forest fires, are keys to realizing the material’s potential as a sustainable alternative.
Many timber buildings are hybrids. Gokhman said the Ascent is being built on a six-story concrete podium, and its stairwell and elevator are being enclosed in concrete. Those elements, along with extra sprinklers, assuaged fire safety concerns, smoothing the approval process for the project’s variances.
Mass timber isn’t fireproof, but several studies have shown the material meets, and in some cases exceeds, fire resistance requirements. Unlike how regular wood-frame construction burns, the laminated layer of engineered timber chars as a large log on a campfire would — a slow process that protects the underlying wood.
Still, even proponents of cross-laminated timber say more fire and structural testing is needed, especially when it comes to exposed timber in towers.
“CLT is still a relatively new product,” said Lionel Lemay, who as an executive with the National Ready Mixed Concrete Association admittedly has skin in the game. “Though some testing has been done, there is still a lot of work to be done to make sure it isn’t part of the problem when it comes to fires.”
Future of timber
Mass timber can drive up project costs by 10 to 15 percent, but Waterstone’s John expects costs to fall as it gains popularity. Chris Sharples, principal of SHoP Architects, which designed a commercial hybrid timber-concrete-steel tower in Australia that will be the world’s tallest, said designing with mass timber can make for more efficient construction timelines.
Materials are manufactured directly from intricate digital models, so that builders are “basically getting a whole kit to a jobsite.” Sharples likened it to a “glorified barn raising.”
“What we believe comes out of that is a lot of the ambiguity, a lot of the reworking, a lot of the quest for more information drops off during the construction process,” he said. “We’re not there yet as an industry, but there are a lot of companies out there that are putting a lot of gray matter into this process, and it is very exciting.”
On the manufacturing side, Europe has the edge. Peronto said developers of larger projects are still more likely to go overseas for wood, noting that the Ascent’s was sourced from Austria. The only U.S. factory that had capacity to accommodate their order was Katerra’s in Spokane, Washington. But it closed in June, and the startup has since declared bankruptcy.
Gokhman said insurance companies remain wary of the material and charge more to insure projects that use it, and some lenders are still uncomfortable with them as well.
Construction workers will also need to adapt to mass timber for it to gain traction. The industry is notoriously resistant to change, especially when it threatens to eliminate jobs. Macdonald’s organization at Oregon State has started working with the Northwest Carpenters Union and plans to develop training programs for contractors.
Susan Jones was an early adopter of mass timber, having designed her family’s Seattle home with the material in 2015. The founder of the architecture firm atelierjones, she represented the American Institute of Architects on the International Code Council’s Tall Wood Building Committee from 2016 to 2019, advocating for upping timber’s height limit to 18 stories.
Her firm is now working on a 126-unit workforce and middle-income housing project in the city. Though excited by the replicability of the project, Jones acknowledged that assembling the expertise and figuring out the supply chain for mass-timber projects is a challenge for developers.
“It can be painful. At this early stage, you need a hand-picked team,” she said.
But her projects could demonstrate timber’s potential.
“If a little five-person firm can figure it out and become a national leader,” she said, “anyone can.”