When engineering giant AECOM started developing a virtual consultation tool in late 2019, its aim was to allow members of the public to weigh in on projects remotely. The idea, at the time, was that busy schedules prevented some from attending critical public meetings.
“It was originally intended for stakeholders who can’t make a physical meeting,” said Kevin Carlson, who leads AECOM’s digital transformation department. “There was no broader thinking” beyond that, he added.
But by the time AECOM released the tool this April, the world had changed.
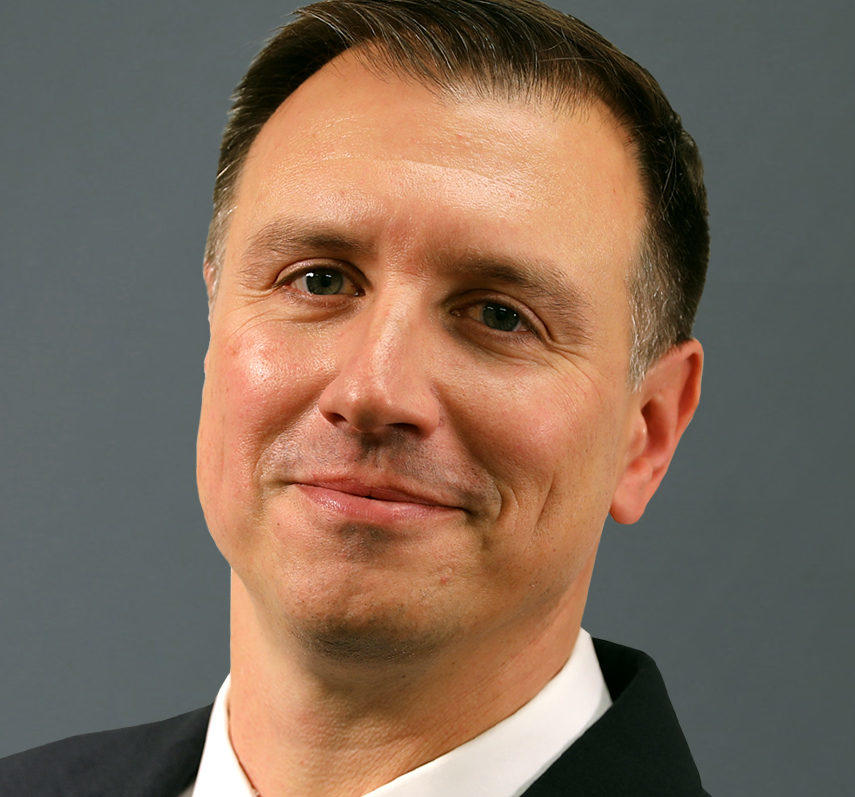
Kevin Carlson, AECOM
The coronavirus crisis created a sudden demand for technologies that enabled public and private meetings to be held remotely — and what was developed as a convenience quickly became a necessity.
Now, as construction sites that were shut down during the pandemic reopen in New York and other big cities, construction companies are facing unprecedented pressures.
From leading firms to smaller contractors, the $1.3 trillion industry must respond not only to immediate safety and health concerns, on top of cost overruns and project delays, but also the need for industry-wide reform.
Industry professionals say construction companies will increasingly need to adopt new technology, as well as alternatives in supply chains and materials to survive an economy heavily impacted by Covid-19.
“That scramble to make up for lost time, and to recover some of the lost revenue is a very real thing that every developer is experiencing right now,” said Alex Elkin, founder of construction consulting firm Eastbound Construction.
“This will be a long-term event,” he added, “and we’re just starting.”
No-luddite land
Even in the short term, the construction industry has had to adjust to new technologies in direct response to the pandemic.
Throughout various sites around the country, project manager Suffolk Construction, which has offices in major cities including New York, Boston, Miami and Dallas, is using monitors that workers wear on their hard hats, for example. The monitors sound alarms whenever workers are within six feet of another.
While there were mixed responses at first, many ultimately saw the value of being able to track contact between construction workers, according to Alex Hall, Suffolk’s executive vice president of business systems.
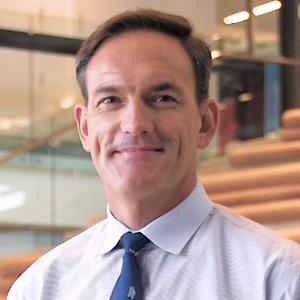
Alex Hall, Suffolk Construction
This was the case on a 518,000-square-foot hotel and condo project in Montana, where a worker was diagnosed with Covid-19, he said. The firm was able to determine who may have been exposed to that person based on whose helmet alarms were triggered.
“As soon as it happens, and the reality of the situation hits home, it changes the psyche on the site,” said Hall, whose company is working on 200 projects nationwide.
Despite the industry’s reputation for being resistant to change, interest in construction-focused tech has grown significantly — from the use of hard hat alarms and drones to 4D and 5D modeling.
Since 2008, investors have poured more than $27 billion into the country’s construction sector, according to the global consulting firm McKinsey & Company.
K.P. Reddy, CEO of Shadow Ventures, an Atlanta-based firm that invests in construction startups, said he thinks the pandemic will help change the industry’s “cultural resistance” to progress in the long run.
Building information modeling, for instance, can allow developers and architects to replan projects delayed by the crisis to potentially make up for lost time and help lower costs. And a number of start-ups offer services that capture images and videos of sites, allowing for remote inspections. Large firms like AECOM and Skanska have even employed robots to perform certain demolition work and bend reinforcing bars.
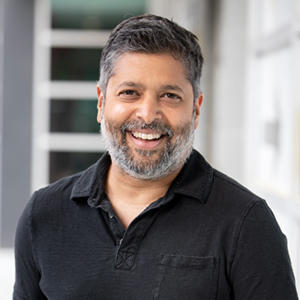
K.P. Reddy, Shadow Ventures
Reddy said tools that automate certain aspects of construction could gain more traction as contractors look for ways to reduce the number of people on a given site.
On a more basic level, the crisis could accelerate the digitization of the construction management process.
“There’s going to be a fundamental reworking of what types of projects get built, and how, as a part of that, every single person in the construction industry, needs to work together,” said Zachary Reiss-Davis, who manages product marketing for Procore, a construction management software company reportedly valued at more than $4 billion.
Barry LePatner, founder of the construction law firm LePatner & Associates, noted that a majority of U.S. construction companies have fewer than 20 employees. He said only companies with deep pockets and larger headcount can afford to consistently invest in new technology.
“You are talking about a small percentage of companies that are better managed, that are trying to move productivity forward,” he said. “While the tech world has gone to great efforts to develop this tech and refine it, the adoption level is significantly lower than it should be.”
AECOM’s Carlson said that while he expects some changes to the construction process — such as remote meetings — to be temporary, he’s found clients to be more open to trying out new tools.
“The comfort level of our clients is increasing. That’s going to enable us to do more in the future,” he said. “We are seeing a shift. The impacts will be lasting, and we’re excited about where that’s going to take us.”
Staggered supply chains
Projects remain under unprecedented scrutiny as construction begins to resume on sites, especially in urban markets.
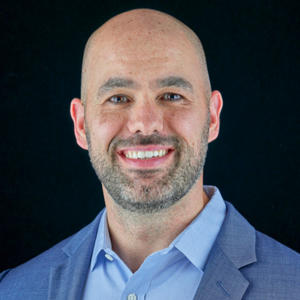
Alex Elkin, Eastbound Construction
Eastbound’s Elkin has been conducting due diligence for lenders and private equity partners concerned about the impact of the coronavirus on project timelines and budgets.
“You’ve got lenders frankly terrified about what’s going on right now,” he said. “The clock has been ticking and that debt service has been accruing.”
The commencement of work on tens of thousands of sites in New York alone will likely put a strain on supply chains as well, further delaying projects.
About 30 percent of building materials imported to the U.S. come from China, according to the construction research and software platform Dodge Data & Analytics.
But many manufacturers have gone out of business due to the pandemic and a growing number of contractors may look to rely less on overseas suppliers. LePatner said he expects supply chains to be disrupted through at least next year, until new manufacturers crop up in North and South America.
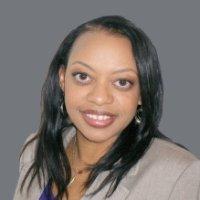
Linda Foggie, Turner & Townsend
Linda Foggie, head of the international construction consulting firm Turner & Townsend’s New York office, said due to the halt in work on sites, supplies haven’t been constrained as much as was initially feared. She said contractors shouldn’t be too concerned about solely buying supplies stateside, but should make sure they have multiple trusted sources for different product types.
“The important thing is that your supply chain is diverse,” she said.
Foggie added that modular and other offsite construction could gain more momentum in major markets like New York, as part of broader efforts to reduce density on project sites.
The market share of permanent modular construction on real estate projects in North America grew by 50 percent between 2015 and 2018, according to McKinsey, though the industry’s share of work remains in the single digits.
During a Zoom panel hosted by The Real Deal in June, Sidewalk Labs CEO Dan Doctoroff argued that city and state regulations need to catch up to advances in construction technology as well.
He pointed to mass timber as a potential cost-saving material that is largely prohibited in the five boroughs, since New York does not allow towers made of the material to exceed six stories.
“There’s a lot of tech and new approaches today,” Doctoroff said. “If government could just get out of its own way, and work with innovators, they could do a lot of amazing things.”