Success in the rapidly expanding field of construction technology appears to hinge on dreaming big. Just not too big.
For Social Construct, a San Francisco-based startup attempting to revolutionize how multifamily buildings are planned and built, success would also depend on dreaming at the right time. The company was finishing its first ground-up project in Oakland in the spring of 2020 when construction sites across the country went dormant with the onset of the pandemic.
The company, which raised $17 million from Founders Fund, Y Combinator and others in 2019, needed additional capital. But it couldn’t get even local investors to cross the Bay Bridge to look at its software-optimized floor plans, plumbing and electrical systems, according to co-founder Michael Yarne.
“We were hoping to have closed on that raise in the fall,” Yarne said. “As you can imagine, that was the worst time.”
Construction technology, or con-tech, has lagged behind the broader proptech market in raising capital, but activity in the space has ramped up significantly since 2018. Some 1,500 con-tech firms have entered the scene since 2009, and about 10 percent of them have gone out of business, according to Unissu, a proptech data and research firm.
Trouble seems to scale with ambition, as evidenced by the spectacular collapse of Katerra, a con-tech unicorn that raised more than $2 billion from SoftBank, in June of this year. Like Social Construct, Menlo Park-based Katerra hoped to transform how multifamily buildings are built — in its case, through a combination of efficient offsite manufacturing and prefabrication.
Katerra’s bankruptcy “cast a pall” over con-tech, said Elie Finegold, a proptech veteran and venture adviser.
“It really can’t be overstated, the impact that Katerra’s collapse had, simply because of the way they built that company — the speed and the noise with which they built it, the acquisitions they made to build it up,” Finegold said.
Katerra’s bankruptcy spooked Social Construct’s investors, who were already rattled by the pandemic, according to Yarne. It didn’t help Social Construct’s case that renters were fleeing urban areas during the lockdown, and the future of cities was thrown into question.
Perhaps most significantly, seeing Social Construct through completion of its first project had taken more than three years — an eternity in venture capital, where investors demand hypergrowth. Manufacturing and construction has nowhere near the multiples and profitability levels that software has.
“The timeline for real, lasting change is so long that I don’t know if venture money is patient enough,” Yarne said.
Social Construct was ultimately forced to shutter this summer. Although its closure was a blip next to Katerra’s bankruptcy, and the reasons for each company’s failure differed — Katerra’s fundamental problem wasn’t so much a lack of funding as how the company spent it — together they highlight the struggles con-tech firms face in attempting to reinvent how the fragmented and hyper-local construction industry builds.
The nut to crack
Con-tech aimed at fundamentally altering the physical makeup of buildings, which, according to Yarne, is a “much harder nut to crack” than easily scalable software solutions. Construction management platform Procore Technologies, for example, has successfully attracted big-ticket investors, and it raised $634.5 million in an IPO in May that priced above the expected range. Procore’s second-quarter revenues of $122.8 million were up 28 percent year-over-year.
There are typically 10 or more separate trades working on a construction site installing a range of systems, including plumbing, electrical, heating and cooling. The technology also has to be customizable to jibe with local building codes, which vary from state to state and city to city. New technologies have to be woven into that web of subcontractors who, because of the sheer demand for their services, have little incentive to change how they do things.
The pandemic may have marked a significant turning point in those attitudes. While the construction industry was relatively slow within the industry to adopt tech, it has recently begun to embrace large-scale change, according to Steve Weikal, of MIT’s Center for Real Estate.
Weikal sees the ongoing labor shortage, as well as investors’ heightened focus on sustainability, as an opportunity for con-tech to shine.
“I think the industry is much more receptive to tech now because they realize these tools lower injury rates, increase quality and shorten the length of time to get stuff built,” he said.
Strength in numbers
Con-tech fundraising actually increased overall during the pandemic, and 2021’s capital raising is on track to surpass 2018’s peak figure of $2.06 billion, according to Unissu. Insiders say that the best opportunities in the field today lie in project-specific efficiency solutions rather than in reinventing the wheel.
James Dearsley, co-founder of Unissu, advocates for a practical approach that promotes step-by-step reformation of existing processes. Technology that promises incremental efficiency gains in the supply chain or project management, for example, is more likely to be embraced by contractors.
Dearsley and others see momentum in 3D printing. In August, the Austin-based startup ICON raised $207 million in a Series B round, more than tripling its equity funding to date. The company recently rolled out a new system capable of printing homes of up to 3,000 square feet twice as fast as it could previously.
Insiders still see opportunities in modular construction, where contractors can control the build environment and thereby improve worker safety and process efficiencies.
“The construction industry is structured in such a way that it factors in tiny margins,” Dearsley said. “I think offsite manufacturing and modular building are going to go an awfully long way to improving the efficiencies.”
So will collaboration, industry leaders say. In August, Volumetric Building Companies, a Philadelphia-based modular construction outfit that specializes in apartment buildings, bought Katerra’s manufacturing and office assets in Tracy, California. CEO Vaughan Buckley attributed the company’s success — 20-fold growth in the past four years, according to the company — to its collaborative rather than subversive approach to technology.
Katerra was vertically integrated “to the point of exclusion,” Buckley added. Instead of attempting to supplant architects and general contractors on the job site, Volumetric wants to provide them with better tools and systems and has voluntarily shared information with other industry players.
No single con-tech company is going to reinvent how people design and build structures, Buckley added.
“There is no secret sauce to disrupt a multitrillion-dollar industry,” he said. “The companies that suffer the most are the ones that are trying to do it alone.”
Too much, too soon
Many of the con-tech firms that have failed or struggled tried to do too much, too soon, according to Zach Aarons, co-founder of proptech-focused venture capital firm MetaProp. He attributed Katerra’s collapse to its having spread itself too thin.
“They were trying to innovate and build products for every piece of the construction value chain,” he said. Instead of sourcing lumber from a specialist, Katerra built out its own mill. Instead of relying on Procore’s project management software, it built its own. At one point, the company planned to manufacture its own appliances.
Founders need to have a “big vision,” Aarons said. “But simultaneously, it’s also important for the founder, at least initially, to be really, really focused on being the best in the world at one thing, and then hoping that they can land and expand from there.”
MetaProp, which launched in 2013, has been investing in con-tech since its inception. Recently, it has put money into such materials science and 3D printing companies as Branch Technology, which fabricates building facades.
The firm is also investing heavily in robotics companies, including PaintJet, Canvas and Built Robotics — specialists in large-scale structure painting, drywall hanging and grading work, respectively.
“You’re going to see more and more autonomous vehicles on the job site — either fully autonomous or controlled via remote control,” Aarons said. “Imagine having a war room where you’re managing 10 construction sites and all the grading, hauling and excavating machinery on those sites, at once. That is a lot of efficiency gain, theoretically.”
Read more
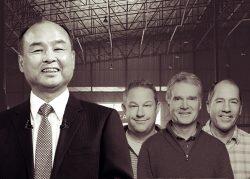
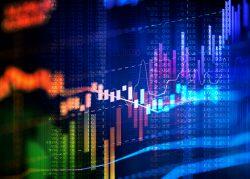