Trending
How 3D-printed homes could solve the housing crisis
Construction could save on money, time, and labor
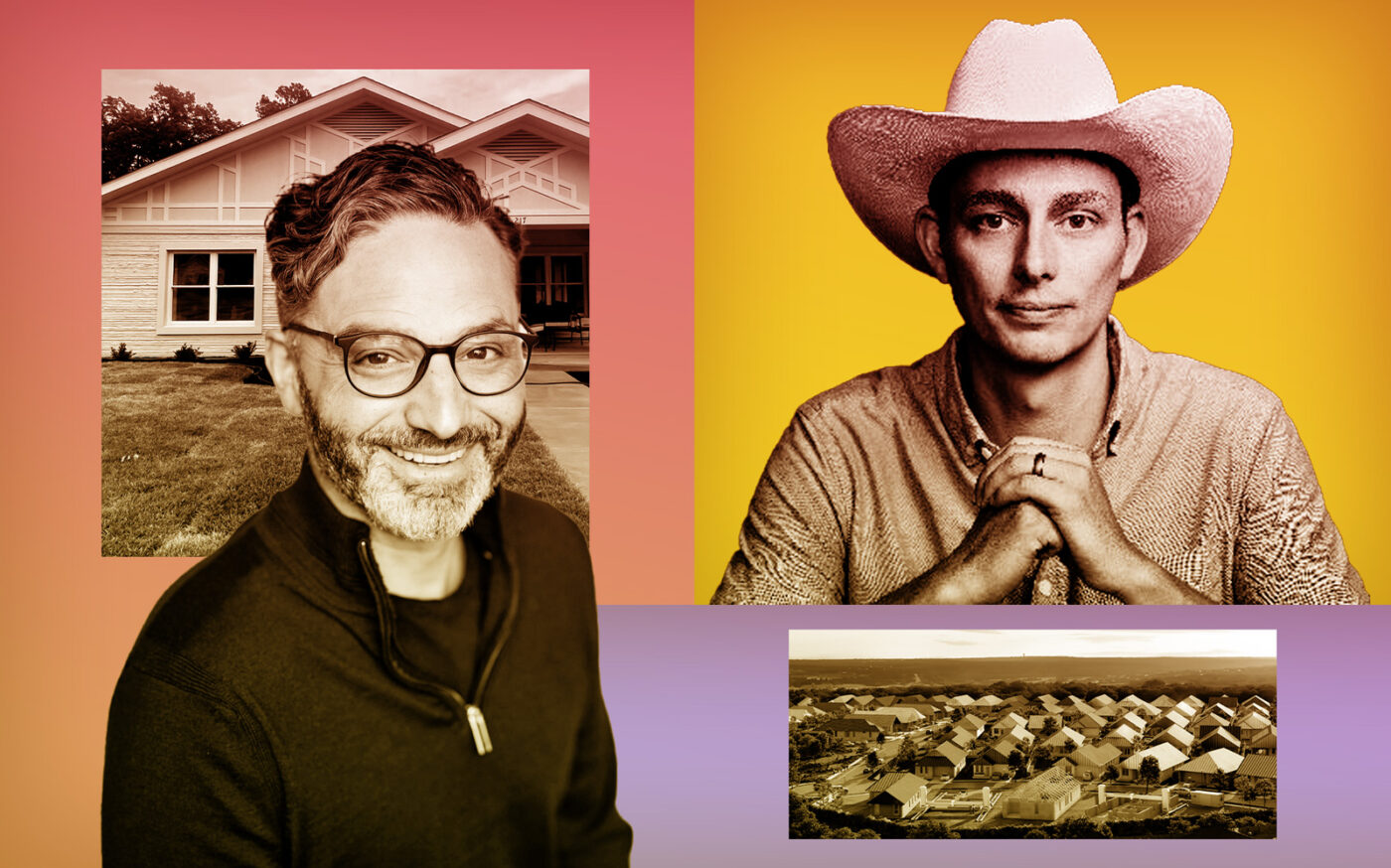
The technology is still in its early days, but 3D printing homes have the potential to dramatically reduce the time, money and materials needed to build houses.
Companies like Alquist 3D and Icon are working on 3D printing technology to construct walls and building components, according to the Smithsonian Magazine. The advances in 3D-printing construction tech have potential to speed up the production of homes amid a protracted housing crisis, with the shortage of homes estimated in the millions.
Aside from the shorter construction time and fewer materials needed, experts also say 3D printing requires fewer construction workers, a boon during the current labor shortage.
Alquist 3D, which is headquartered in Greeley, Colorado and led by founder and chairman Zachary Mannheimer, partnered with Habitat for Humanity to build 3D-printed homes. In one case, it took just 40 hours to construct the walls for a 1,300-square-foot house, the outlet reported.
“We suspect the eventual cost to print future 3D homes for Habitat would be around $180,000 to $190,000,” Janet Green, the CEO of Habitat for Humanity Peninsula and Greater Williamsburg, told the publication.
Alquist is partnering with Habitat for Humanity to 3D-print 100 homes in a Colorado development.
Icon, which is based in Austin and led by founders Jason Ballard, Evan Loomis and Alex Le Roux, has a 100-unit project just outside its hometown. The firm partnered with homebuilding giant Lennar to develop 100 3D-printed single-family homes as part of the Wolf Ranch by Hillwood master-planned community. Sales launched for the printed homes in June, with prices ranging from $475,000 to $570,000, and floor plans spanning between 1,600 and 2,100 square feet.
–– Kate Hinsche