
Building buildings in New York City is challenging for many reasons.
Written By: Marty Waisbrod President & CEO | Promont, Smarcon & Latitude Compliance
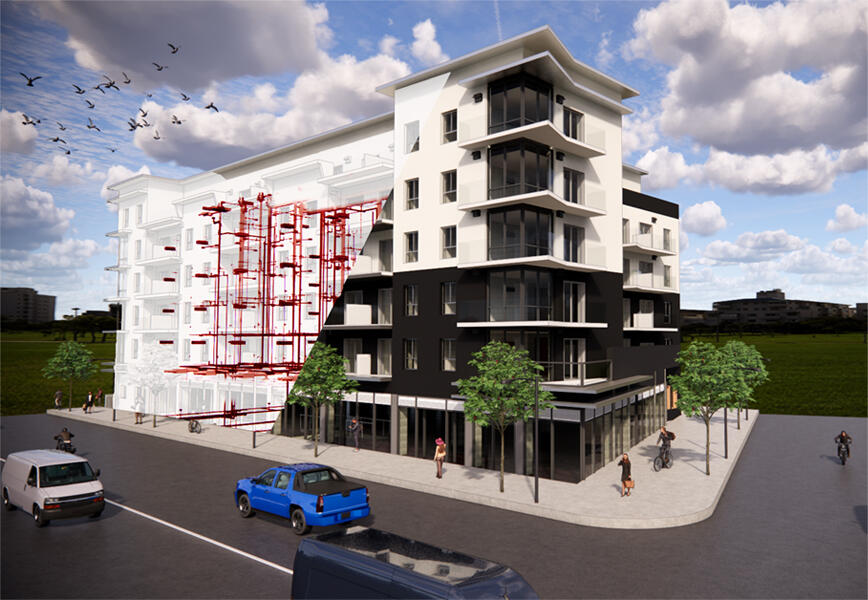
As the president and CEO of an NYC-based general contracting firm (Promont.nyc), I’ve seen that first and foremost, the most difficult things to navigate are often the ones we can’t do anything about, such as tricky building codes or even complaints from difficult neighbors.
However, there are some things we can change. As general contractors (GCs), how many times have we relied on architects, designers and engineers to coordinate our construction drawings, only to find too many mistakes after it was too late? How many times have you released steel for fabrication based on approved shops, only to realize that the approved shops were seriously lacking? In my case, the answer is way too many times. Too many times I have had to swallow the cost of mistakes happening on jobs, and too many times I have lost time because of a lack of coordination.
Recently, I decided to do something about it. I now use building information modeling (BIM) for all of my jobs. I made the decision to return the power back to the people — the GCs. Using BIM allows our teams to visualize everything before we build it. It allows us to detect any possible clashes when they’re still on paper — when there is still something we can do about them. It allows for all trades to properly coordinate their work and make sure no one gets in anyone else’s way.
We also use BIM to create real-life drive-throughs of the job so that both ownership and our management teams can see and feel what the project will look like. This helps ownership see if there is something that bothers them so they can choose to fix it before we start the work.
Consider this case study from my company: We were recently working on a steel structure building that included many pieces of curved steel, as the project contained a number of curved walls to create a semi-circle structure. The steel plans looked pretty good on a 2-D drawing and would’ve looked just as good on a 2-D shop drawing. Had we, as the GCs, allowed that work to commence just based on the 2-D drawings, we would’ve experienced many mistakes and delays. The 3-D BIM model generated more than 30 requests for information, or obvious clashes, missed connections and incorrectly sized members, just to name a few.
Using the BIM model allowed us to discover these RFIs, and the fixes were already prescribed in the RFIs themselves. All that remained was approval from the engineer of record. Once the fixes were approved, we fed the fixes into the model, which automatically updated the drawings building-wide to reflect those changes.
If you’re considering using BIM, there are a few things to keep in mind in order to leverage it effectively. First, engage with it early in the preconstruction stage. Once there is a design development set done, start the BIM process right away. Use BIM to build one “master” model that includes all trades. Then, after you have completed the “clash detection” part of the process, individual trades are then able to receive fully coordinated shop drawings directly from the model. If you approach BIM this way, any changes that inevitably come out in the construction document set will be relatively simple; you will easily be able to modify your model and see what changed and how it might impact the job.
I’ve also learned that using BIM as just another set of plans generated by someone who doesn’t understand the construction part of the business and is targeting BIM from the design side would be a mistake. BIM is designed to help us, the GCs, build better and faster. The only way we can do that is if we approach BIM from the construction side and build the building virtually the way we would build it in real life. This will allow your team a better understanding of the job, its complexities and its challenges, as well as help you take advantage of any approach or methodology that will help you build a better building before putting a shovel in the ground.
However, it’s important to note that BIM is a very large and somewhat complicated platform. It has tremendous amounts of information and capabilities built into it. Sometimes, I’ve found companies marketing BIM services don’t fully understand all of its capabilities themselves. This led me to start my own BIM company, Smarcon. Smarcon was founded as a BIM company that is local, knowledgeable and above all construction oriented. We approach the BIM process from the GC’s point of view. “How can we best build this building?” Is the starting point of everyone of our BIM projects. Our clients are developers demanding their GC’s use BIM to make sure that change orders are reduced or better yet eliminated, architects and engineers that want their final CD plans to be perfect so that they don’t face unhappy clients when the inevitable mistakes are made and GC’s, like me, who are tired of losing time and money to mistakes that could’ve easily been solved using BIM.
BIM is a very small cost component of today’s construction projects and I’ve personally found it to be worth my investment for any project that comes our way, regardless of size. From my perspective, not embracing this technology would be equivalent to an architect still drawing plans by hand and not using computer-aided design. Depending on your role in a construction team, you could find different value, benefits and challenges with using BIM. Just remember to keep a few best practices in mind to ensure you’re leveraging it effectively.