Assembly OSM, a modular construction startup that has compared its process to putting together Ikea furniture, raised $38 million in Series A funding.
The company was founded in 2019 by twin brothers Bill and Chris Sharples, principals of Manhattan-based SHoP Architects. Assembly calls its construction method “post-modular” because it is more akin to a car or aircraft assembly line than a traditional modular build-out, where the structure is put together on a single factory floor.
Assembly instead spreads construction across a vast network of suppliers and manufacturers — an approach that “constrains” the process but allows for more freedom in design, CEO Andrew Staniforth said.
The startup has now raised more than $60 million. Fifth Wall’s climate tech fund and Bessemer Venture Partners’ Rob Stavis led the latest round, with participation from the Jefferies Group, Manta Ray Ventures, FJ Labs, RSE, Signia, Gaingels, New Vista Capital, Tectonic, Atento, Etan Fraser and Moving Capital.
The Fifth Wall fund is “dedicated to decarbonizing the built environment and the global real estate industry.” Assembly claims that its buildings can have 30 to 40 percent less embodied carbon than traditional ones and that its construction sites cut emissions by 60 to 70 percent.
The allure of modular construction is relocating much of the building process to an indoor, controlled environment with a consistent workforce. But as a relatively young industry, it is far from being perfected.
Many firms are trying to work out the kinks of modular construction. Assembly, which is doing feasibility work in New York, San Francisco, Los Angeles, St. Louis and other cities, is no stranger to setbacks. It had been planning four Manhattan buildings with 800 apartments, but Staniforth said these were feasibility studies for projects that Assembly ultimately did not pursue because of the pandemic and other factors.
Read more
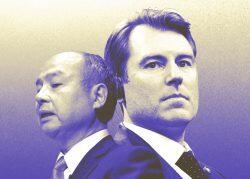
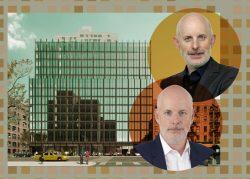
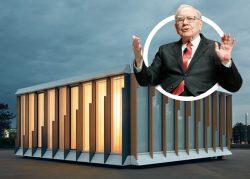
Staniforth worked at Forest City Ratner Companies when the firm was building its ballyhooed B2 project, a 32-story modular tower, only to see it bogged down by litigation, cost overruns and leaks. He said Assembly’s people can assure developers and investors that they “know what went wrong on that project.”
“It is a big, important statement that we can make because we lived through that project,” he said.
The highly publicized failure of another modular startup, Katerra, which filed for bankruptcy last year, has not discouraged Assembly. Staniforth said one of the easiest ways to combat the “Katerra stigma” is to point out to developers and investors that Assembly’s approach is “the exact opposite.”
Katerra had a vertically integrated business model, setting out to control every aspect of the construction process by acquiring architecture, engineering and construction management firms and by opening its own factories.
The approach required massive infusions of capital, was wracked by delays and proved unsustainable.
“In our world, we have redundancy,” Staniforth. “We have multiple suppliers for each of the components.”